In the petrochemical industry, where large-scale maintenance is both routine and critical, Shutdowns, Turnarounds, and Outages (STO) projects stand out as particularly high-stakes operations. These projects necessitate a temporary halt in operations to perform essential maintenance, upgrades, or repairs on crucial equipment. While these activities are vital for long-term operational efficiency, STO management comes with significant risks and costs. This is why having a solid plan is crucial and the role of a cost engineer during the preparation phase becomes invaluable.
Understanding STO Projects: High Stakes and High Costs
Shutdown, turnaround, and outage (STO) projects are akin to a high-stakes poker game. If not managed properly, they can lead to massive financial losses, extended downtime, and missed production targets. The challenge lies in completing the work as efficiently and cost-effectively as possible, ensuring the facility is back up and running quickly and safely. This is where a cost engineer shines, acting as the financial guardian of the project, ensuring every penny is spent wisely.
What Does a Cost Engineer Do During STO Preparation?
The preparation phase of an STO project is all about setting the foundations right, meticulous planning and anticipating every possible scenario. A cost engineer is at the heart of this process, making sure the financial side of things is well under control. Let’s dive into the key roles and responsibilities of a cost engineer:
1. Creating a Realistic Budget and Cost Estimate
In a STO project, one of the first tasks for a cost engineer is to develop a detailed cost estimate. This is not just about putting a rough number on a page; it’s about creating a comprehensive financial plan that will guide the entire project.
Historical Data Analysis: Cost engineers often start by looking at historical data from previous STO projects. For instance, if the last turnaround involved significant costs due to equipment rentals, that information helps in anticipating similar costs in the current project.
Work Scope Definition: It is crucial to define exactly what work will be done. For example, if the project involves replacing a critical heat exchanger, the cost engineer will collaborate with the technical team to ensure all related tasks such as dismantling old equipment, installing the new unit, and testing are accounted for in the budget.
Cost Breakdown Structure (CBS): To prepare a CBS the cost engineer then breaks down the budget into detailed components. This might include labor, materials, equipment rentals, and even contingency funds for unexpected events, like a sudden need to replace equipment.
By the end of this process, the cost engineer ensures the budget is realistic, detailed, and aligned with the financial goals of the organization.
2. Managing Vendors and Contracts
STO projects often involve multiple vendors and contractors, each with their own costs and challenges. The cost engineer’s job responsibilities includes managing these relationships to keep the project financially on track.
Contract Review and Negotiation: The cost engineer reviews contracts to ensure they are fair and aligned with the project’s financial goals. For instance, if a contractor’s quote seems high, the cost engineer might negotiate better terms or seek alternative suppliers. Therefore, the involvement of a cost engineer is crucial in the bidding and tendering phase.
Vendor Cost Management: Throughout the project, the cost engineer monitors vendor costs to ensure they stay within budget and all the potential costs are accounted in the budget. This includes everything from material costs to the services provided by external parties.
By keeping a close eye on these relationships, the cost engineer helps prevent cost overruns and ensures the project delivers value for money.
3. Optimizing Resource Allocation
STO projects often require a vast number of resources, from skilled labor to specialized materials to dedicated equipment’s. The cost engineer works closely with the project team to make sure these resources are used optimally and efficiently.
Labor Cost Management: For instance, if the project requires highly skilled welders, the cost engineer will estimate labor costs, considering factors like overtime pay and shift differentials. They also work to prevent costly inefficiencies, such as overstaffing during periods of low activity.
Material Cost Control: Materials can be a significant expense and managing this cost is crucial. If the project requires specialty valves that need to be imported, the cost engineer ensures these materials are ordered in time to avoid delays and cost escalations due to expedited shipping.
By allocating resources wisely (e.g., using Resource Breakdown Structures to categorize and track resources), the cost engineer keeps the project on track and within budget.
4. Identifying and Planning for Risks
STO projects are full of uncertainties. What if a crucial piece of equipment fails during the process? What if bad weather delays critical work? The cost engineer’s responsibility here is to foresee these risks and plan accordingly.
Risk Assessment: The cost engineer helps create a risk register, a comprehensive list of potential risks, categorized by their likelihood and potential impact. For instance, if there’s a history of delays due to late material deliveries, this would be a high-priority risk.
Contingency Allocation: Once the risks are identified, the cost engineer sets aside contingency funds. For example, if there’s a risk of needing additional labor due to unforeseen complications, money is allocated to cover this without breaking the budget.
This risk analysis ensures the project can handle surprises without causing financial chaos.
5. Setting Up Cost Tracking and Reporting Systems
Once the budget is set, it is not just a matter of letting the project run on autopilot. The cost engineer is responsible for setting up systems to track and report on spending throughout the project.
Baseline Cost Establishment: The cost engineer sets a baseline, which is essentially the financial roadmap for the project. Every expense is measured against this baseline to ensure the project stays on course.
Cost Reporting Framework: Regular reports keep everyone in the loop, from the project manager to the executive team. For example, if labor costs are trending higher than expected, these reports allow for timely adjustments before costs spiral out of control.
This ongoing monitoring ensures the project remains financially healthy from start to finish. To dive deeper into how this process works in practice, check out our blog on project cost tracking.
Conclusion
At its core, the role of a cost engineer is about more than just numbers. It is about making informed decisions that impact the entire project and, ultimately, the organization’s bottom line. Through careful planning, risk management, and resource allocation, a cost engineer ensures that an STO project is not just completed, but completed efficiently, safely, and within budget.
In essence, the cost engineer acts as the financial steward of the project, balancing the need for meticulous cost control with the realities of complex, large-scale operations. Their expertise helps to ensure that STO projects not only meet their objectives but do so in a way that is financially sustainable and aligned with the long-term goals of the organization.
If you are looking for a robust solution to enhance your STO planning and execution, try Cleopatra Enterprise’s Work Pack Management Software. With features that streamline work pack preparation, track progress, and integrate safety and QA/QC, and more, Cleopatra helps you achieve your STO project goals with ease.
Before starting a cost estimation for a technical project, it is important to have the knowledge of both…
Just like it is important to have contract templates in your contract management software, you also need to…
Related resources
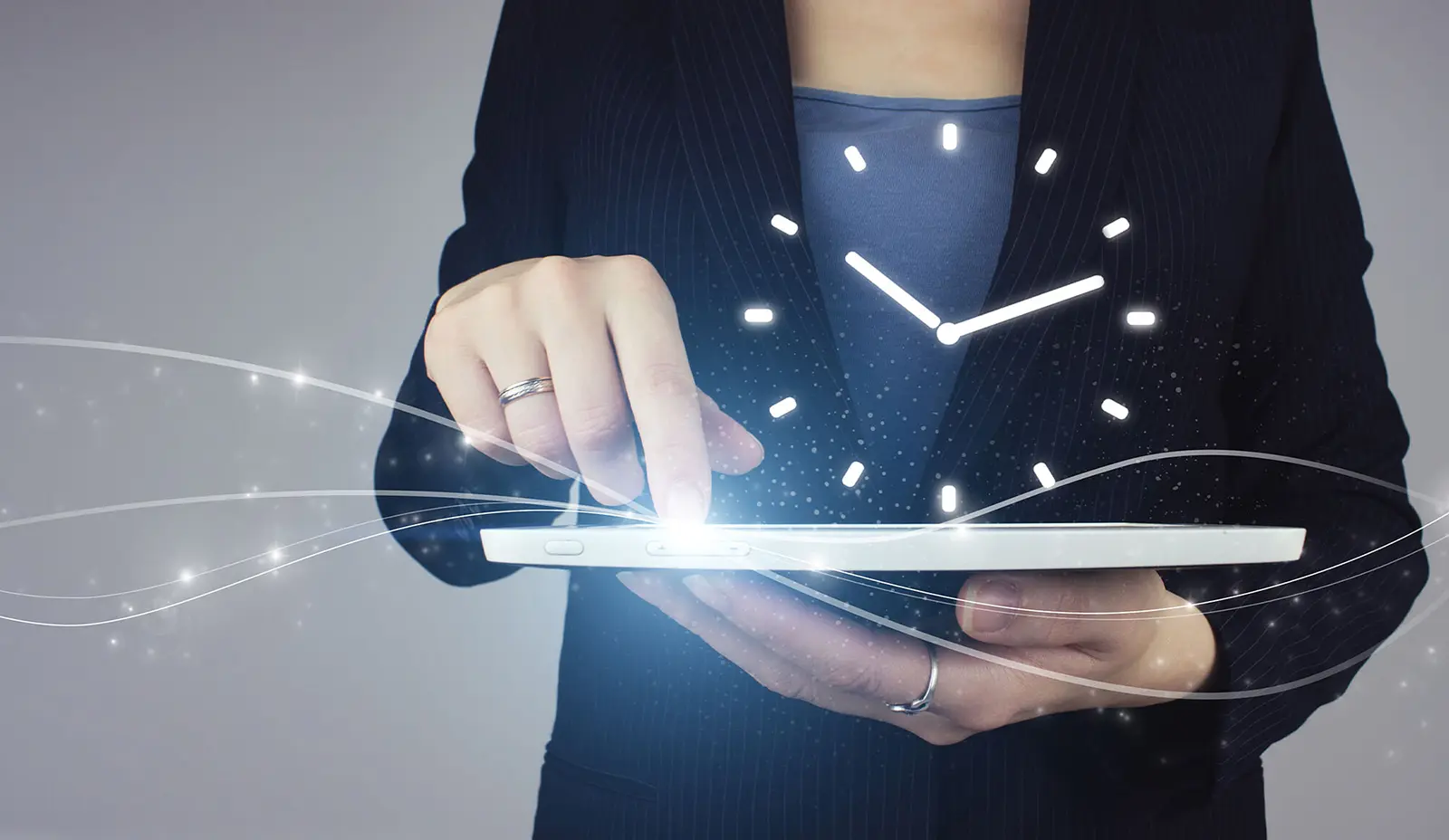
Work Pack Management Software
Keep construction and turnaround teams aligned with Cleopatra Enterprise's work pack planning software. Prepare a more efficient and safer way of working.
Keep construction and turnaround teams aligned with Cleopatra Enterprise's work pack planning software. Prepare a more efficient and safer way of working.
Read page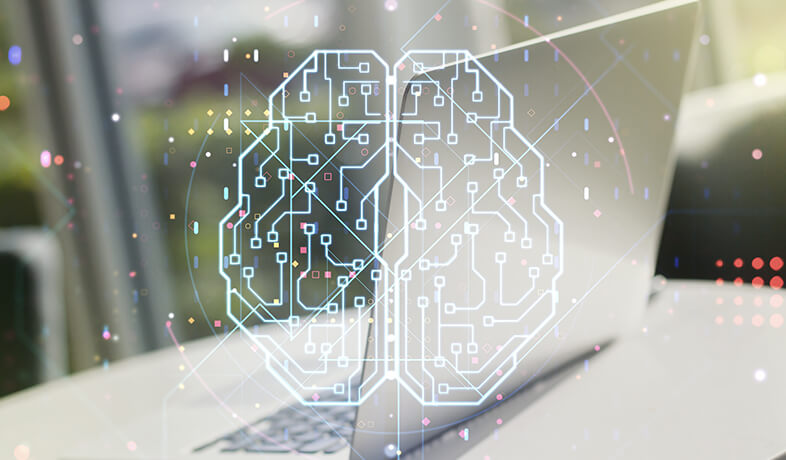
Work Breakdown Structures (WBS): the correct philosophy
Dig into the Work Breakdown Structures for assigning the work-packages / deliverables and apply the correct cost control philosophy.
Read blog article