Turnarounds (TARs) are essential yet costly maintenance events in industries like oil and gas, chemicals, and manufacturing. These planned shutdowns demand extensive resources, manpower, and logistical coordination. However, when a turnaround is postponed or canceled at the last minute—due to financial constraints, lack of planning progress, supply chain disruptions, regulatory issues, or unforeseen operational constraints—it can lead to significant financial and operational setbacks. To mitigate these cost impacts, companies must adopt a proactive and structured approach that balances financial control with operational flexibility.
Optimize Contractual Agreements
Vendor and contractor commitments often represent the most immediate financial risk when a turnaround is delayed. To minimize these risks, companies should structure contracts with flexibility in mind. This includes incorporating cancellation clauses, milestone-based payments, and risk-sharing agreements that distribute financial exposure. Negotiating force majeure and delay clauses can also help reduce penalties and allow for rescheduling without incurring major costs. To better understand which contract types provide more flexibility, consider reading our blog on different types of contracts for turnarounds.
Engaging legal teams early to draft flexible agreements, diversifying vendor relationships to provide alternative options, and considering framework agreements that allow adjustments in scope and timeline without major cost escalations can further enhance resilience against last-minute changes.
Implement a Phased Procurement Strategy
A postponed turnaround does not necessarily mean that materials and equipment should go to waste. To avoid unnecessary financial commitments, companies should adopt a phased procurement strategy. Delaying non-essential purchases until closer to the execution date can help minimize inventory liabilities. Also, negotiating return and restocking agreements with suppliers ensures that excess materials can be sent back with minimal penalties. Vendor-managed inventory programs can also be leveraged to reduce holding costs, as suppliers can retain ownership of critical spare parts until they are needed.
When a turnaround is postponed last-minute, at least 80% of its required materials would have been purchased. However, by utilizing a consignment stock agreement, the company can significantly reduce storage costs and re-purpose inventory for ongoing maintenance activities. Classifying materials based on urgency, partnering with suppliers on flexible delivery schedules help optimize procurement decisions and prevent unnecessary expenditures.
Optimize Workforce Planning
Labor costs can be a major financial burden when a turnaround is postponed, as delays may result in idle workforce and contractual liabilities. Staggering hiring and mobilization efforts can help prevent bringing in contract workers too early, thereby reducing unnecessary labor costs. Companies should also develop a standby or redeployment plan to ensure that skilled workers can be reassigned to other ongoing projects if needed. Also, negotiating early exit clauses with contract labor providers can help minimize demobilization fees in case of unexpected delays. For more details on the topic, read our dedicated article on Optimizing Workforce Planning for Large-Scale STOs.
Improve Inventory, Logistics, and Infrastructure Management
Properly managing materials, logistics, and deployed infrastructure can prevent unnecessary expenditures when a turnaround is postponed. Whenever possible, companies should prioritize in-house storage options to avoid costly third-party warehouse fees. Rescheduling transportation instead of canceling outright can also help minimize logistical penalties. Additionally, materials that have already been delivered can be reallocated to other ongoing or upcoming projects to avoid waste. A proper strategy for all the existing scaffoldings, rental equipment, facilities, and storage facilities needs to be developed to minimize the cost impact.
Strengthen Financial and Budgetary Controls
A well-structured financial plan can help absorb unexpected cost shocks from turnaround delays. Companies should implement scenario-based budgeting that accounts for postponements and maintains contingency reserves specifically for turnaround-related disruptions. Tracking committed versus actual costs in real time ensures that financial exposure is continuously monitored, and spending can be adjusted dynamically.
Setting up an early-warning cost tracking system, engaging cost and finance teams regularly to reassess budget allocations, and identifying cost-saving opportunities in non-essential expenditures like temporary facilities can further help manage financial risks.
Enhance Stakeholder Communication and Change Management
Turnaround postponements affect multiple stakeholders, making clear and proactive communication essential. Internal teams—including operations, maintenance, finance, and procurement—must remain aligned to ensure smooth rescheduling. Engaging external partners, such as vendors, suppliers, and logistics providers, early in the process can help minimize penalties and facilitate renegotiations. Workforce morale should also be managed through transparent communication, ensuring that employees understand the rationale behind changes and remain engaged.
A turnaround postponement or cancellation does not have to translate into massive financial losses. By adopting a structured, proactive approach—focusing on contract flexibility, strategic procurement, stakeholder management and communication, workforce agility, and proper financial controls—organizations can minimize cost impacts.
Are you looking to improve your turnaround processes? Discover how Cleopatra’s shutdown, turnaround, and outage software can streamline every aspect of your STOs from start to finish.
Artificial Intelligence (AI) is taking the world by storm. Since the public release of ChatGPT, the internet has…
When it comes to managing Shutdowns, Turnarounds, and Outages (STOs), finding the right local partner can be a…
Related resources
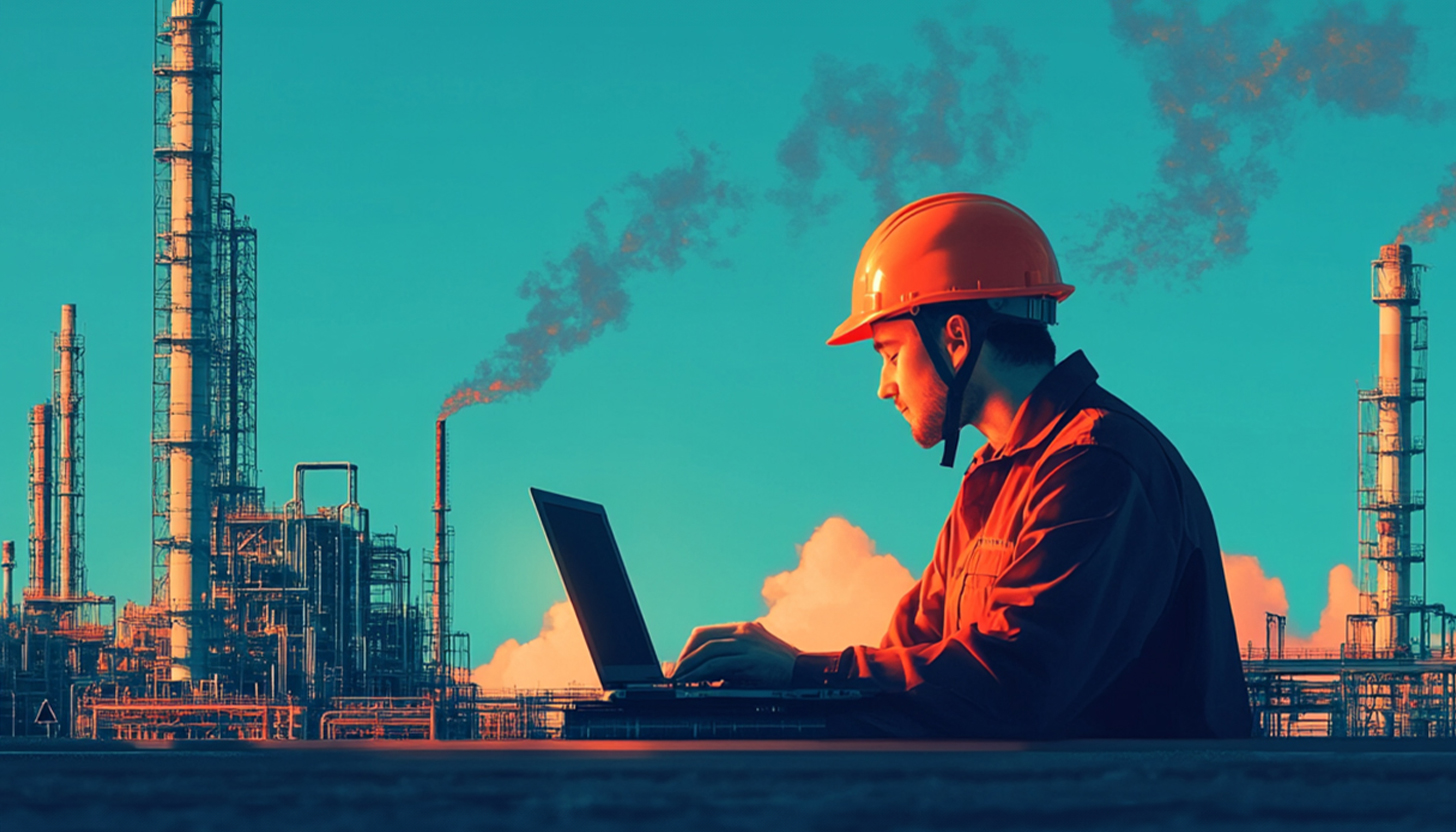
The responsibilities of a Cost Engineer in STO preparation
Learn the vital responsibilities of cost engineers in planning STO projects, balancing budgets, managing risks, and more.
Read blog article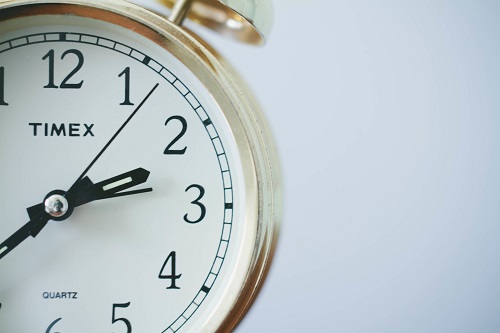
Cost management for turnaround projects, useful or not?
Most of you know that turnaround management is critical for refineries and other petrochemical facilities, as these major events require careful planning and cost management. Turnarounds typically involve significant capital expenses to execute and major operational expenses due to revenue loss when the facility is shut down. As such, they…
Most of you know that turnaround management is critical for refineries and other petrochemical facilities, as these major…
Read blog article