In asset-intensive industries, Shutdowns, Turnarounds, and Outages (STOs) are among the most complex and high-stakes events. They offer a rare window to inspect, repair, and optimize assets, but despite extensive planning, many STOs fall short. Often budgets overrun, timelines slip, and safety is compromised.
What’s often missing? A dynamic and integrated risk management approach. Too many STOs treat risk as a box to check during planning rather than a continuous thread throughout execution. That separation is often what causes well-structured plans to unravel under real-world pressure.
The High Stakes of STOs
An STO can cost a facility hundreds of thousands to millions per day in lost production. For instance, unplanned refinery shutdowns often incur losses of $500,000–$1 million per day, as reported by PetroChem Expert. Add contractor fees, rental equipment, inspections, and penalties, and the financial stakes grow fast.
That’s why months of planning go into each STO. Critical paths are mapped. Schedules are optimized. Crews are booked.
But even strong plans fail if they’re built on static assumptions and lack a system to identify and respond to risk dynamically.
The Planning Fallacy: Where STOs Start to Drift
STO planning often starts with good intentions, but risk management is still treated as a separate layer. This creates fragility.
Common issues include:
• Risk is handled by separate teams and not embedded into core planning.
• Assumptions are treated as fixed, like contractor availability or weather windows.
• Scenario planning is shallow, missing complex interdependencies or systemic delays.
Poor planning-risk integration is a major reason STOs fail. For example, a recent AMACS report found that up to 85% of turnarounds miss their goals due to poor collaboration between owners and contractors.
Why Execution Breaks Without Integrated Risk Management
Once execution begins, STOs become tactical. Without integrated risk visibility, issues escalate quickly:
1. Surprises turn into crises
A major Australian LNG plant in 2019 overran by 5 days after late-stage fouling in heat exchangers required unplanned cleaning. With no early warning, the team scrambled to find vetted crews.
2. Frontline teams become reactive
Supervisors shift from executing to firefighting—managing permit delays, material gaps, or access conflicts.
3. Communication silos cause delays
For instance, at a German petrochemical site, a simple inspection delay in piping held up insulation and painting for three extra days due to a lack of cross-team updates.
4. Safety suffers under pressure
A North Sea offshore facility saw a spike in confined-space injuries during the final days of a delayed 2022 STO. This was linked to fatigue and rushed workflows.
What An Integrated Risk Management Approach Looks Like
Integrating risk doesn’t require more people; it requires a shift in how STOs are run. Here are five core practices that top-performing teams adopt:
1. Dynamic risk registers
Risk logs should be updated daily based on field data, delays, and supplier input, not filed away after early planning.
2. Cross-functional ownership
Risk insights come from all sides—engineering, HSE, procurement, and contractors—not a single team.
3. Pre-mortems and scenarios
High-impact “what-if” cases are explored before execution, including contractor unavailability, late scaffolding, or adverse weather.
4. Leading indicators over lagging data
Monitor precursors like delayed permits or inspection backlogs rather than waiting for incidents to surface.
5. Assigned risk roles
Make risk accountability explicit. Assign clear owners for high-impact risks and involve them in daily progress reviews.
Closing Thought: Risk as a Lens, Not a Threat
STOs will never be free of risk, but the goal isn’t elimination. It’s intelligent and proactive management.
With integrated risk practices, STOs move from reactive firefighting to resilient execution. Teams make faster decisions, adapt with confidence, and protect both budgets and safety because they’ve built risk into every layer of the process.
In the end, the most successful STOs aren’t the ones with perfect plans; they’re the ones that adapt fast, communicate clearly, and manage risk as a living process.
Are you looking to improve your STO processes? Discover how Cleopatra’s shutdown, turnaround, and outage software can streamline planning and execution with integrated risk management. Keep your STOs on time, on budget, and safe, even when the unexpected happens
Shutdowns, Turnarounds and Outages (STO) events often involve project scope, which introduces many challenges. Especially meeting event schedules.…
When it comes to managing Shutdowns, Turnarounds, and Outages (STOs), finding the right local partner can be a…
Related resources
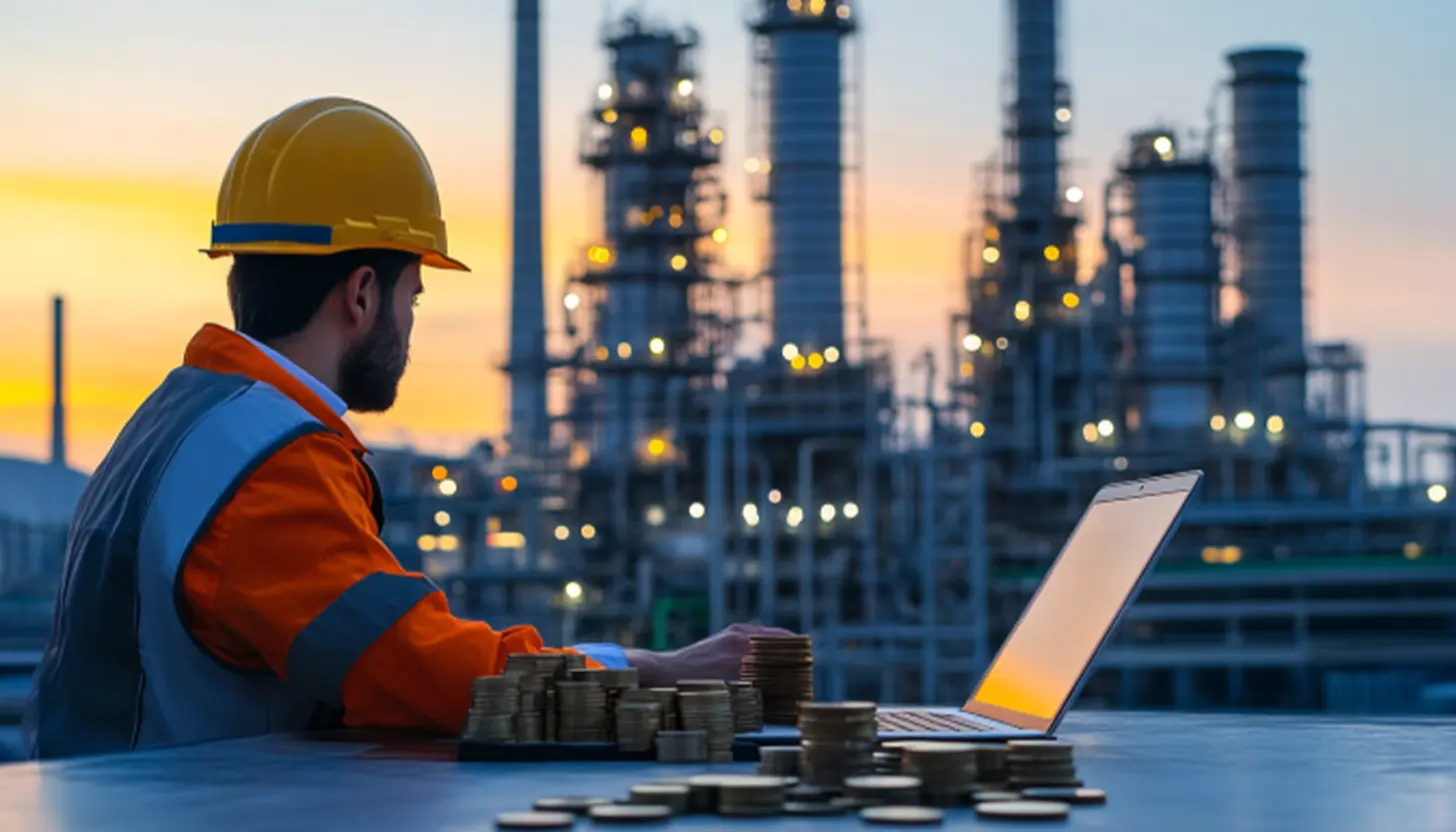
Mitigating cost impact when turnarounds are postponed or canceled
Discover key strategies like flexible contracts and phased procurement to mitigate costs from turnaround postponement or cancellation.
Read blog article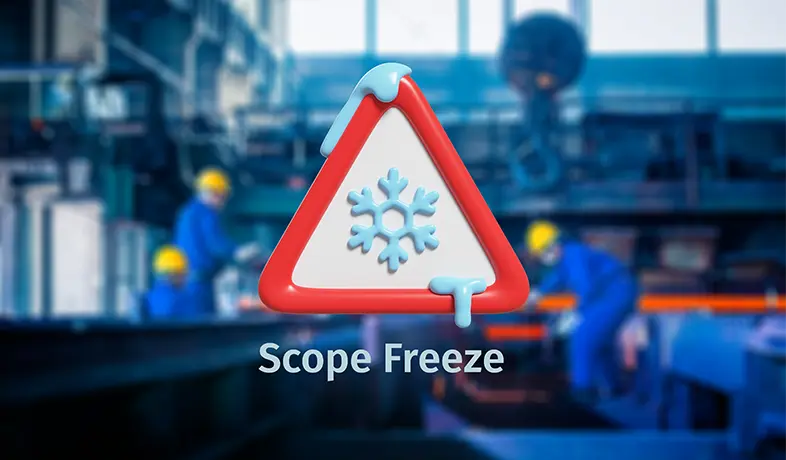
The Critical Role of Scope Freeze in Turnaround Success
Scope freeze is one of the key pillars that separates a successful turnaround from one that runs over budget and behind schedule. This blog explores what scope freeze means in TAR projects, why it's essential for cost and schedule control, when to implement it, and how to manage post-freeze emergencies…
Read blog article